

It will be equipped to repair all products worldwide for all customers. Genmark is expanding its presence in Europe, opening a global repair center in Neufahrn, Germany, near the Munich airport. “This is opening up new markets for us in Asia and is allowing us to increase product development in the advanced packaging market,” noted McMahon. Being part of a publicly traded company has increased customer confidence in Genmark’s longevity. Now a wholly owned subsidiary of Nidec, Genmark retained its brand but gave it a facelift. The company was recently acquired by Nidec, a Japanese company listed on the Nikkei stock exchange. He expects to hit double digits with the number of systems shipped by 2020. He said that as a direct result of exposure from t his 2015 article posted on 3D InCites, five Codex stocker and storage systems have shipped in the advanced packaging market. The company is also looking into non-standard substrate handling, varying from 6-inch wafers to large format panels and everything in between.īut that wasn’t the only good news Carl McMahon, EVP worldwide sales and marketing had to share. It handles the glass wafer while it is being inspected for thickness and uniformity, so that compromised glass wafers can be detected and discarded. Also on display last week at #SEMIEurope was its wafer handling robot. Robots for automatic beer pourers are just a side gig for Genmark Automation. #SEMICONEuropa /fhUn1D3W8UĪ Genmark robot was also being demonstrated as a transport system for glass substrates in temporary wafer bond/debond systems. Is it beer thirty yet? Stop by Nidec at booth A4.659 to enjoy a perfectly poured Hefeweizen. I stopped by Gemark Automation’s to check out the second generation of its beer pouring robot, which I’m happy to say has shaved 8 seconds off its time from generation one. The company has seen an uptick in the last year in interest in the wafer-level packaging segment.
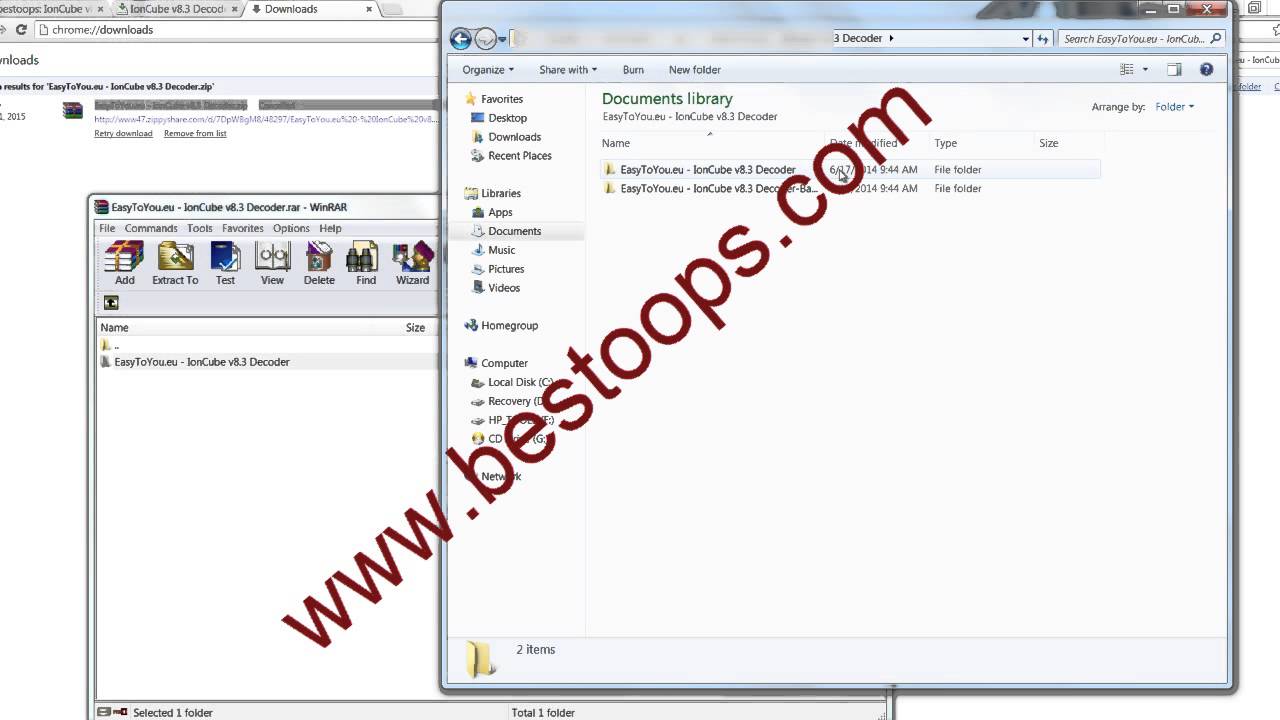

It provides lithography support tool for the steps leading up to and following lithography, including clean, coat and bake, as well as nano-imprint patterning, wet etch, strip, bonding and debonding. Lundstrom said Obducat, based in Switzerland, supports both the front-end and advanced packaging markets. The rotating covered chuck allows for that to happen. The key is to avoid turbulence during the spin process to reach a thinner and more uniform coat and have the same amount of material in the center as at the corners, with only a 5-10mm edge exclusion, explained Lundstrom. In the Obducat booth, CEO Patrik Lundström and his team showcased the company’s solution to this issue: a spin coater that uses rotating cover chuck technology (RCC) to spin coat uniformly on square substrates up to 1.5m in diameter, at a target thickness of ~ 500nm. People were using slit coating, which doesn’t create a thin or uniform enough layer for the lift-off layer. In particular, depositing lift-off layers thinly and uniformly on a rectangular substrate is a challenge yet to be solved by spin-coating. In fan-out panel level packaging applications, one of the identified pain points is in the lithography steps for patterning the RDL layers. Patrik Lundström, CEO, Obducat, shares booth space with Keith Cooper, NXQ. While the tool is targeted to the back-end,Ait-Mahiout says the company will “touch the front end” with the same tool. Designed for HVM environment, the system can be configured to inspect wafers up to 300mm, including thin wafers, reconstructed wafers, and wafers mounted on dicing frames.
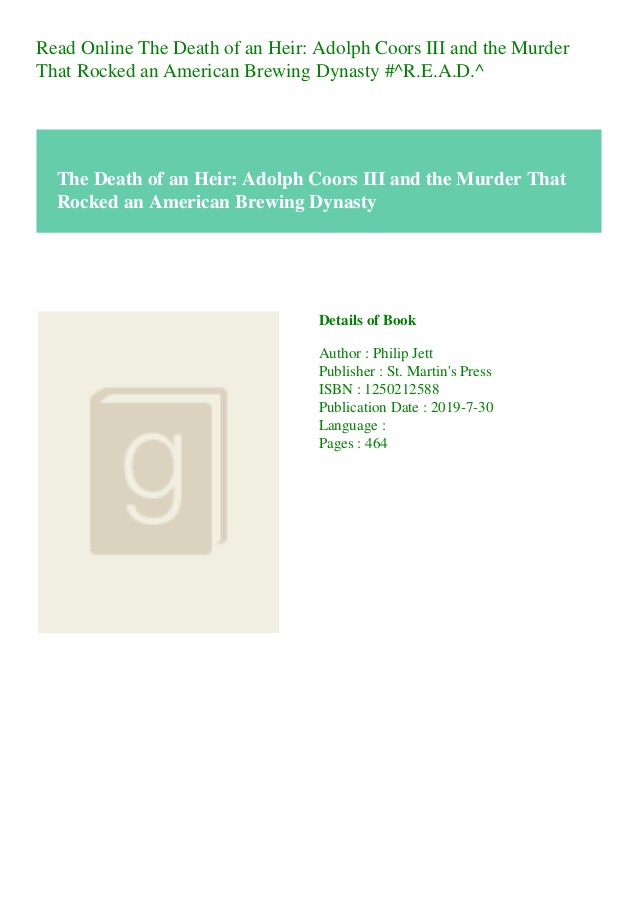
This “tool that sees everything” uses new illumination optical sensors combined with proprietary algorithms to detect things like shorts and opens on RDL and residues on bump top and bond-pads that lead to field failures. Ait-Mahiout said that as wafer level packaging feature sizes continue to decrease, OSATS need inspection systems for high volume manufacturing that can detect defects in bumps, micro-bumps, and redistribution layer (RDL) down to 2µ l/s. This first-generation Light-IX platform was conceived to fill a gap for today’s outsourced semiconductor assembly and test (OSAT) suppliers. It’s also part of the company’s overall strategic plan to cover a broader scope of inspection and metrology needs with fewer platforms. He talked about the company’s latest tool introduction, the UnitySC Light-IX, which is the first platform to implement technology gained as a result of the HSEB acquisition early in 2018. Kamel Ait-Mahiout, CEO of UnitySC, was one of those who was pleased about the event’s co-location with Electronica, as it provides attendees with more of the supply chain. UnitySC CEO, Kamel Ait-Mahiout (center) conducts business at the booth.
